I materiali compositi sono frutto dell’ingegno dell’uomo nel saper individuare le proprietà di alcuni specifici materiali e nell’applicare le metodologie corrette per poterli “mixare”. Si tratta, infatti, di materiali non omogenei nati dall’unione di materiali diversi. I singoli materiali che costituiscono il composito vengono detti costituenti, dei quali uno è in veste di matrice, l’altro è in veste di rinforzo.
Consideriamo i materiali compositi più famosi, ossi le cosiddette“fibre di”. Parliamo delle arcinote fibre di carbonio (C), fibre di vetro, fibre ceramiche e fibre aramidiche, meglio conosciute come kevlar. Si tratta di materiali dall’altissimo valore tecnologico, molto costosi e non riciclabili (anche perchè non destinati al largo consumo). In ciascuno di essi, la matrice è la fase continua del materiale, e può essere costituita da una resina polimerica, da un metallo o da un ceramico. Il rinforzo è la fase discontinua, ossia i filamenti fibrosi da cui il composito prende il nome, la cui disposizione all’interno del corpo conferirà le ottime caratteristiche di resistenza.
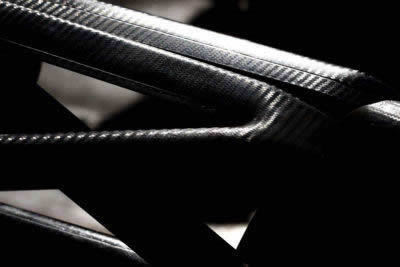
L’anisotropia, cioè il comportamento meccanico non omogeneo ma ottimizzato in base della direzione di sollecitazione di progetto (con le fibre disposte in maniera da resistere prevalentemente in tale direzione), e la leggerezza, ne fanno materiali di riferimento per gli impieghi in campo aerospaziale, automobilistico, ciclistico e motociclistico, sportivo competitivo e biomedico.
FOCUS: LA RIVOLUZIONE DEI TELAI IN F1
La Fibra di Carbonio è un materiale composito modernissimo, ma “antico” per ciò che riguarda il confronto con la sua categoria (la prima applicazione è databile al 1958). Questo fa sì che sia forse il più noto e certamente il più diffusamente impiegato. Biciclette da corsa ad alte prestazioni, appendici aerodinamiche e persino canne da pesca sono “carbon fiber” , ma un tempo l’introduzione di questo materiale fu una grande rivoluzione persino per un ambiente sempre tecnologicamente all’avanguardia come la F1.
Parliamo dello sviluppo dei telai. Il telaio è la struttura portante di un automobile, nel cui pianale (la parte bassa) sono alloggiate le masse non sospese (il gruppo ruota), motore, trasmissione e scarico. Quando non risulta separato dalla carrozzeria, si parla di scocca portante. In F1 il telaio centrale costituisce la struttura principale sulla quale vanno ad installarsi tutte le altre componenti. Essa avvolge il cockpit, cioè è il vano con il quadro comandi in cui alloggia il pilota. Si capisce bene che, oltre ad avere una funzione fondamentale dal punto di vista aerodinamico, esso è decisivo per la sicurezza del pilota in quanto deputato a proteggerlo dalla forza di eventuali urti.
Alla fine dei gloriosi anni ’70, i telai delle monoposto erano a traliccio di tubi in acciaio con pannelli di alluminio rivettati. Pensare simili veicoli spinti da motori V12 a 300 km/h fa capire qualcosa sul coraggio di chi li guidava.
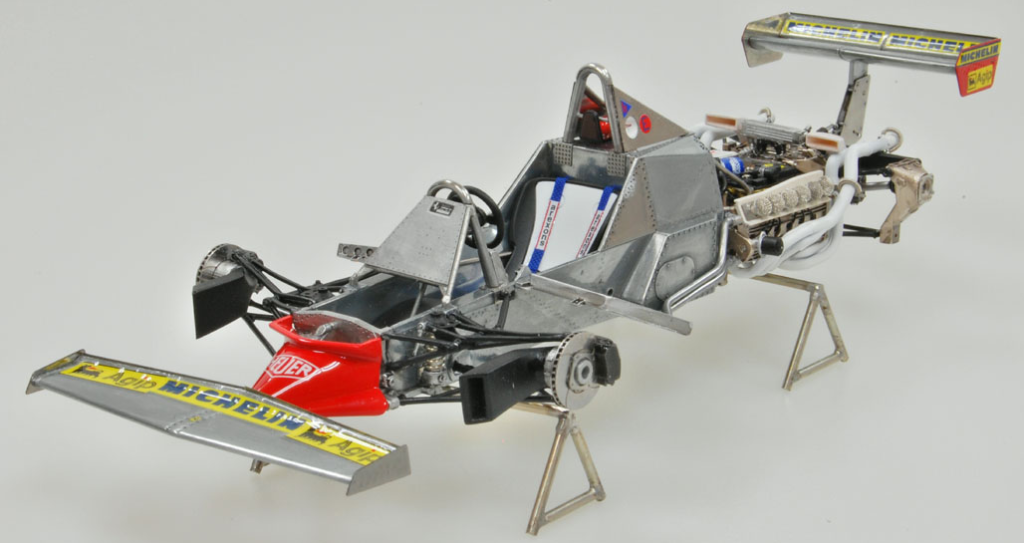
La rivoluzione in questo campo fu dettata dal telaio monoscocca centrale in fibra di carbonio, introdotto sulla mcLaren MP/1 dal progettista John Barnard nel 1981. “Monoscocca” significa che la struttura è un corpo unico. Questa modalità di realizzazione è resa possibile dalla malleabilità della fibra di carbonio. Per rendere malleabili i metalli è necessario molto calore (le temperature di fusione non sono quasi mai basse), mentre il carbonio, prima della sua cottura (operazione che gli conferisce rigidezza), è poco più rigido di un tessuto e questo permette di modellarlo secondo le forme volute. Le capacità di resistenza meccanica e l’assenza di soluzioni di continuità fanno della monoscocca una migliore cellula di sopravvivenza.
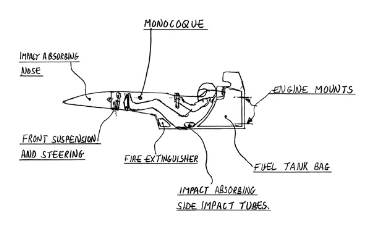
Più sicuro e più leggero, quindi (la fibra di carbonio pesa 1/4 dell’acciaio e 1/2 dell’alluminio). Ma non solo. Il telaio monoscocca in fibra di carbonio si ottiene, infatti, disponendo fogli di materiale secondo uno schema a “sandwich” (carbonio – nido d’ape – carbonio), e questo garantisce una maggiore rigidezza senza compromettere la leggerezza (tanto più una struttura è spessa, più questa è rigida: è per questo che si utilizzano le travi a doppia T in edilizia, per tenere il materiale più lontano dall’asse neutro, la linea che scorre al centro della trave). Questa rigidezza è fondamentale per ridurre la torsione in curva.
Immaginiamo la monoposto vista dall’alto, e facciamo finta che abbia la forma di un rettangolo, con le sue dimensioni B<L. Individuiamo il baricentro G e consideriamo un asse orizzontale perpendicolare a L passante per G. Se immaginassi di applicare una coppia di forze che sollecitino il rettangolo con asse del momento coincidente con l’asse orizzontale, il rettangolo si opporrebbe per sua natura di corpo fisico alla sollecitazione mediante il momento di inerzia, funzione cubica di L. In breve, se la massa è l’inerzia (resistenza alle variazioni dello stato di moto) di un sistema nei riguardi di una sua traslazione, il momento d’inerzia è l’inerzia del sistema verso la sua rotazione. Se aumento L cresce il momento di inerzia, vale a dire che la sezione rettangolare risulta più resistente alla flessione: il momento di inerzia è il parametro di rigidezza di una sezione.
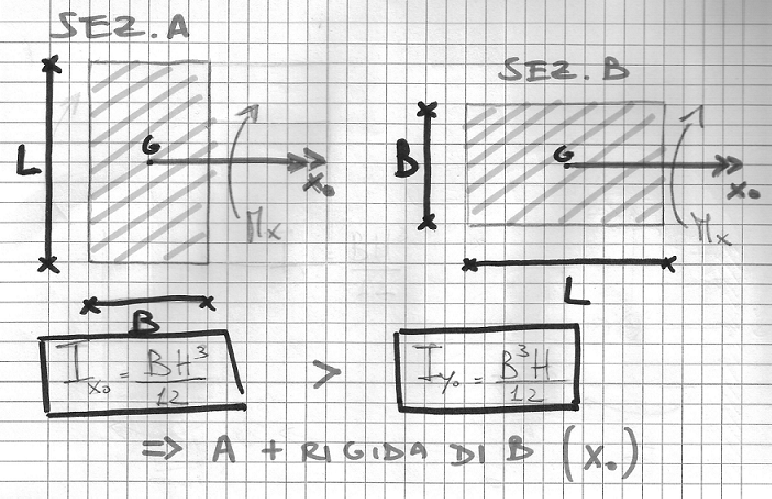
Di conseguenza, cambiando prospettiva ed immaginando le sollecitazioni avvenire con asse del momento coincidente con l’asse di imbardata, cioè un asse verticale perpendicolare a G attorno al quale il corpo può cambiare direzione, ruotando, deduco che un telaio costituzionalmente più rigido offre una maggiore inerzia torsionale, cioè una maggior capacità di opporsi al momento torcente (cioè alla coppie di forze esercitate dagli pneumatici durante la percorrenza in curva attorno all’asse di imbardata), e dunque una migliore reattività con cui la vettura risulta in grado di cambiare direzione!
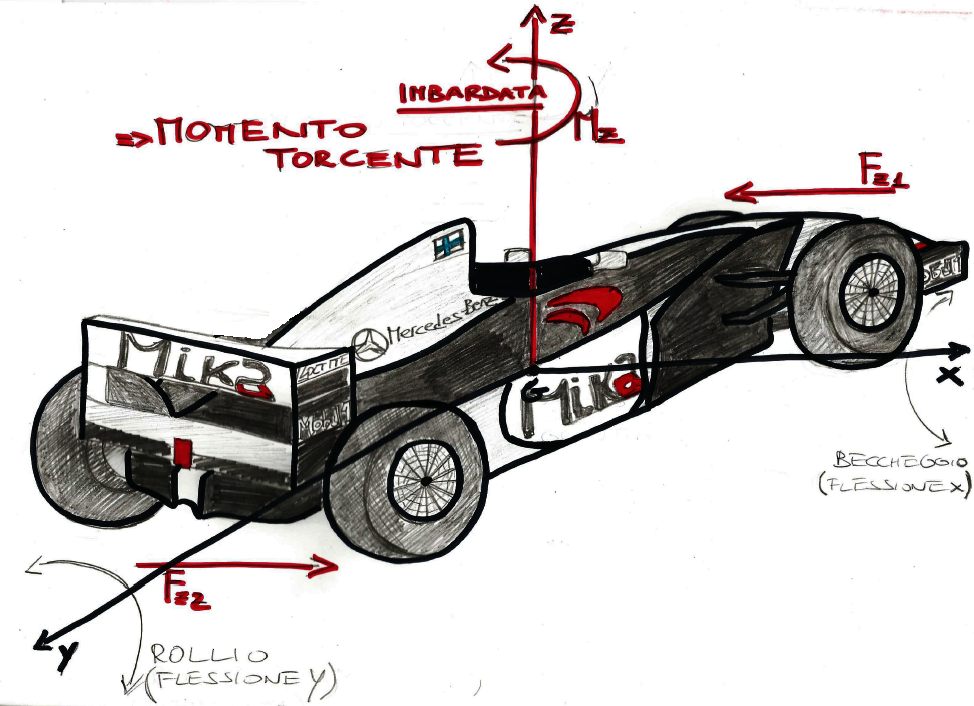
In conclusione, nel video, godiamoci il telaio monoscocca nella F1 moderna!